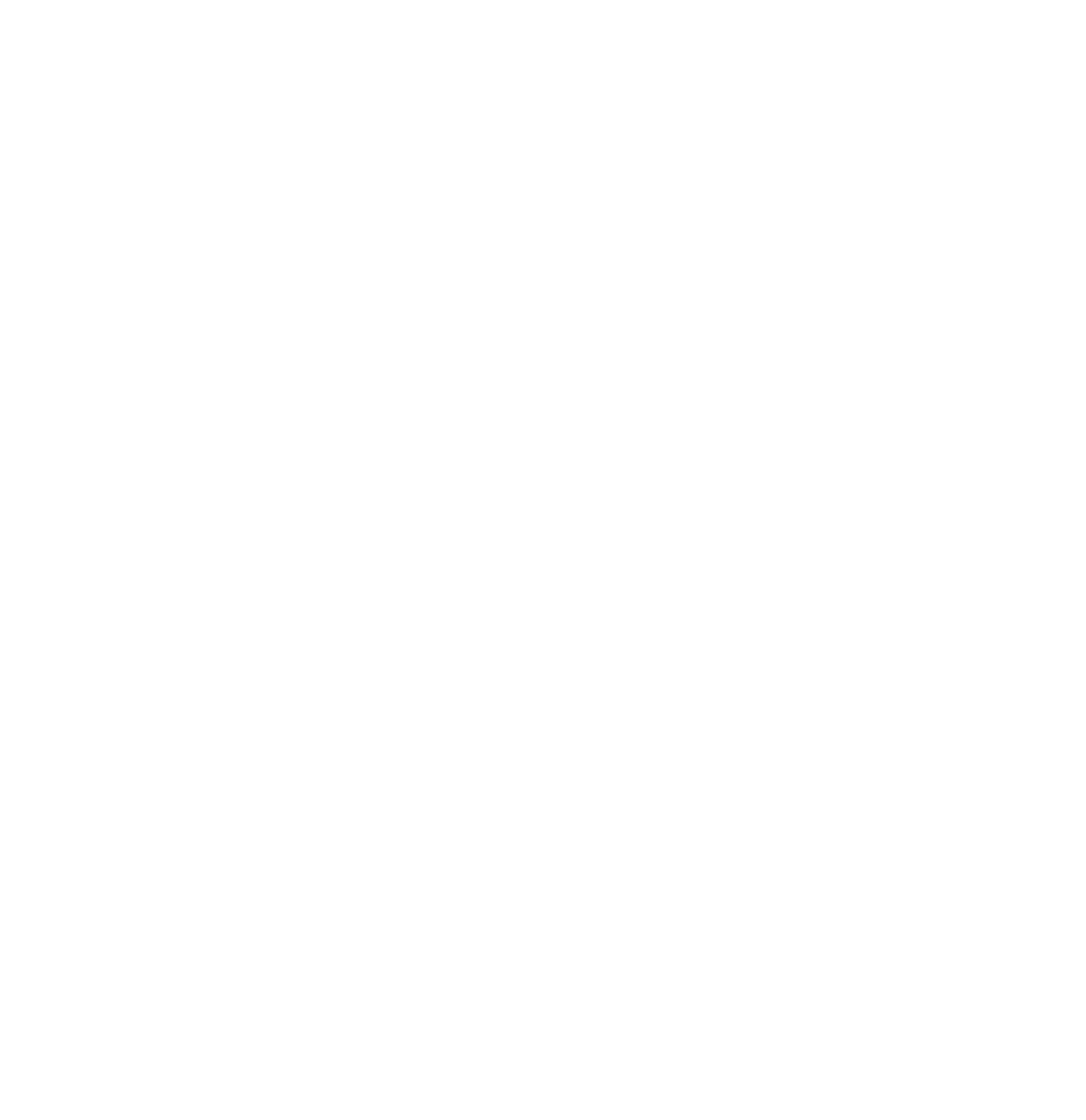
print Big, print Strong, print Fast
If we can 3D print a motorcycle in a week, what can it do for you?
build envelope (x|y|z): 400mm|400mm|300mm
machine dimensions (W|D|H): 690mm|785mm|725mm
speed: up to 2kg per day
materials: PA12-CF, PA12-GF, PETG-CF, 95A Flex
power: 120v AC 1800W
weight: 97 kg
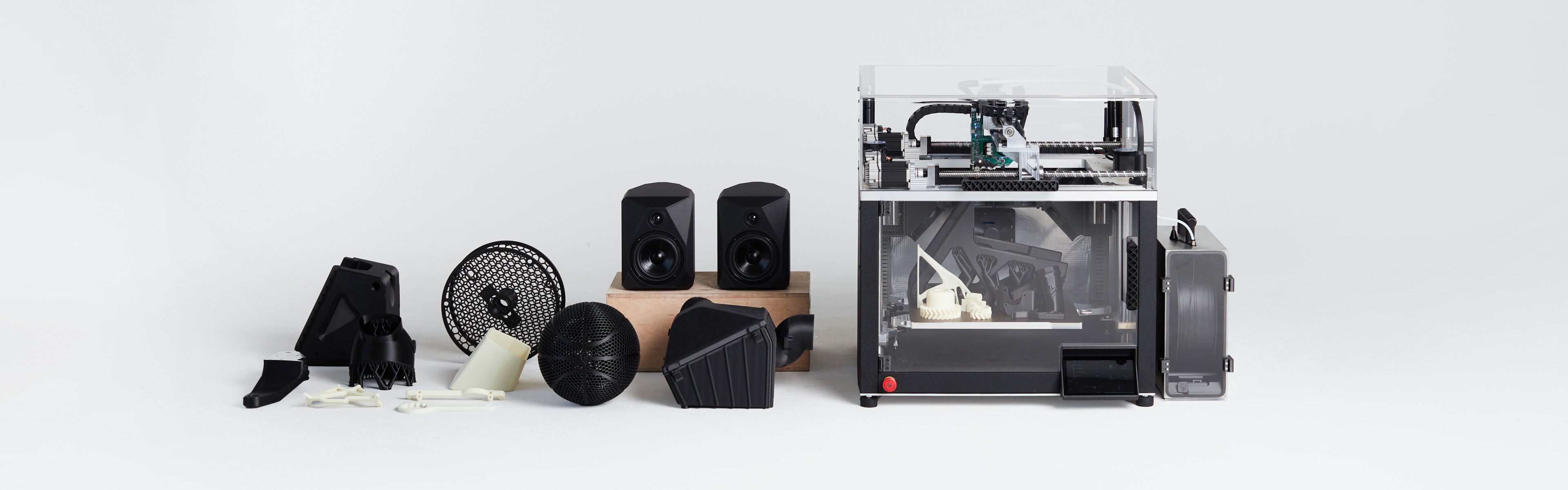
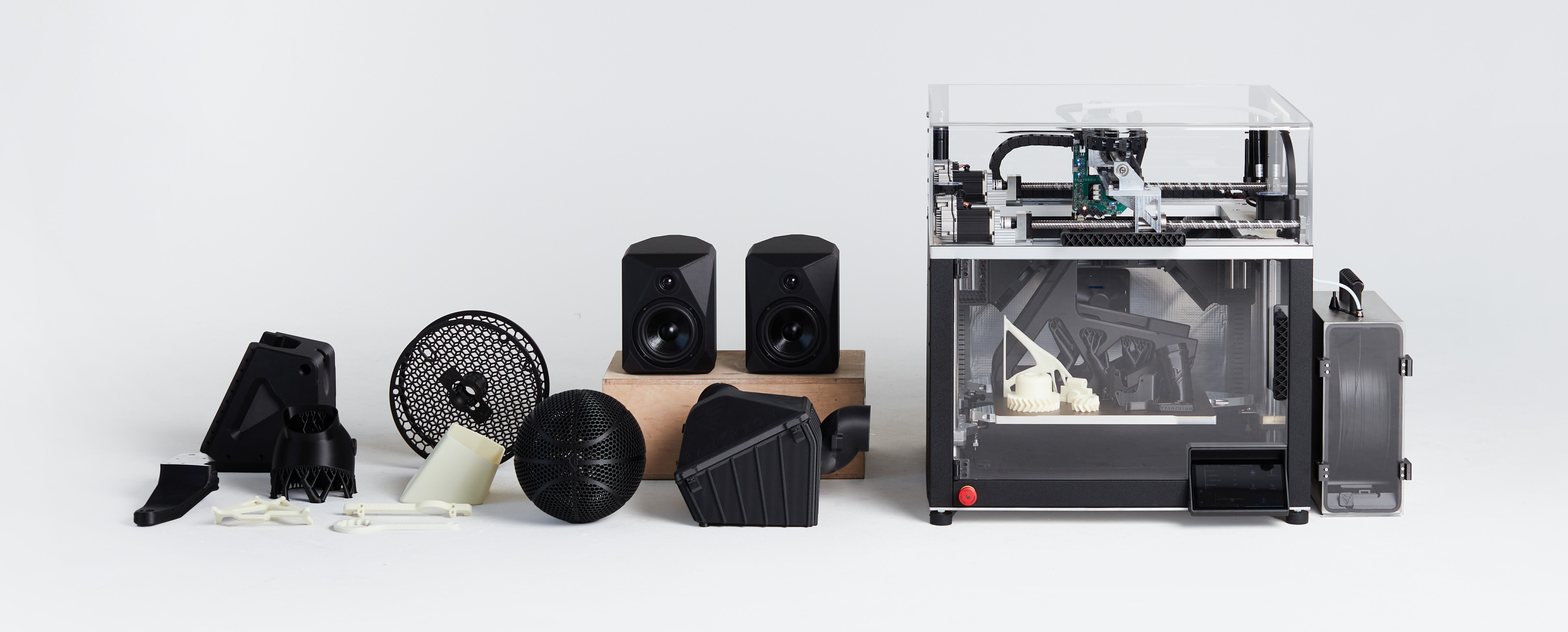
HS-Pro Overview
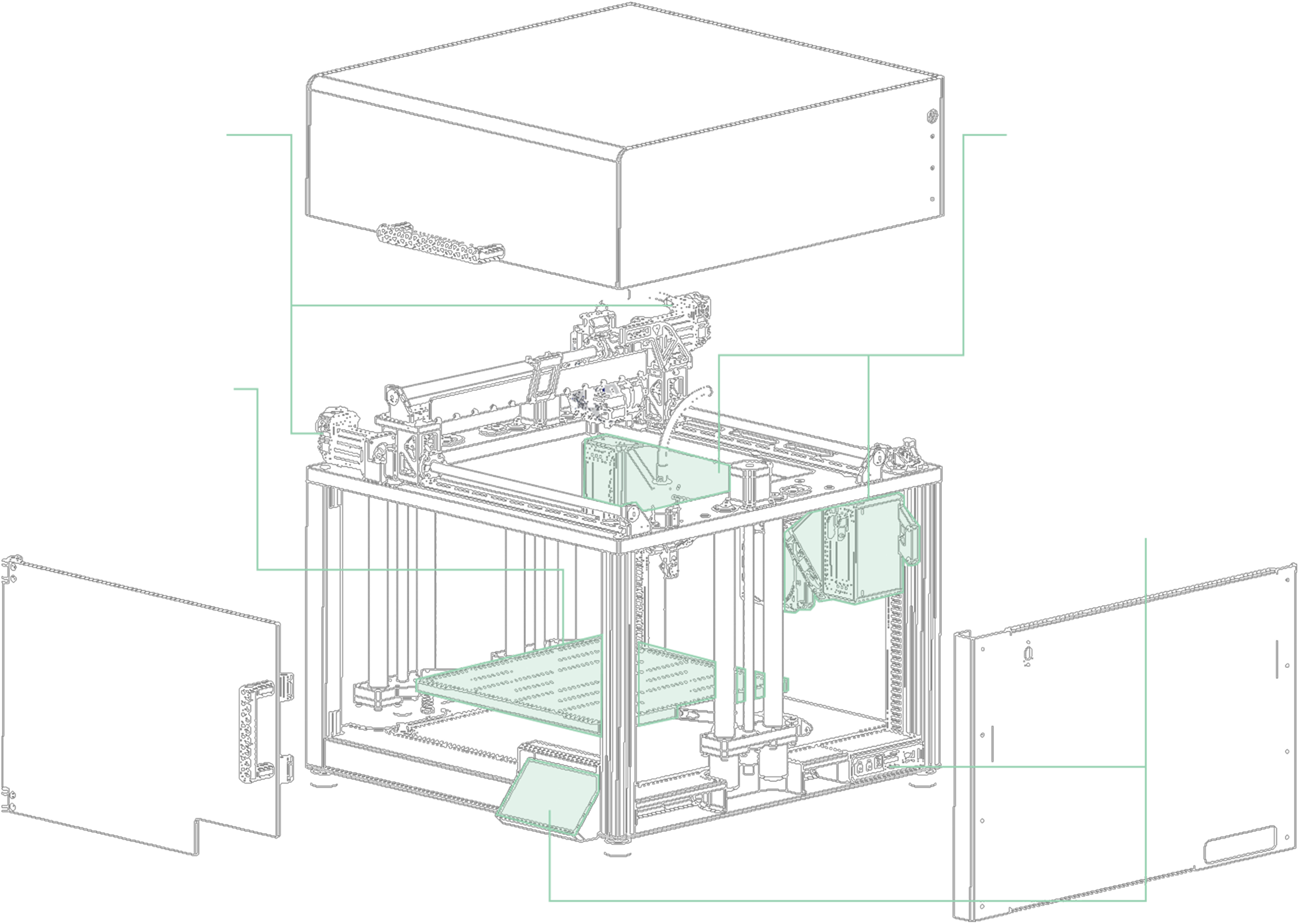
Hot = Strong
Cold to hot in 5 minutes
Don't compromise on quality and speed
Intuitive interface
WIFI + ethernet + USB
Hardware Airgap avalible
Print Big Parts
(15.75” x 15.75” x 12”)
HS-Pro Overview
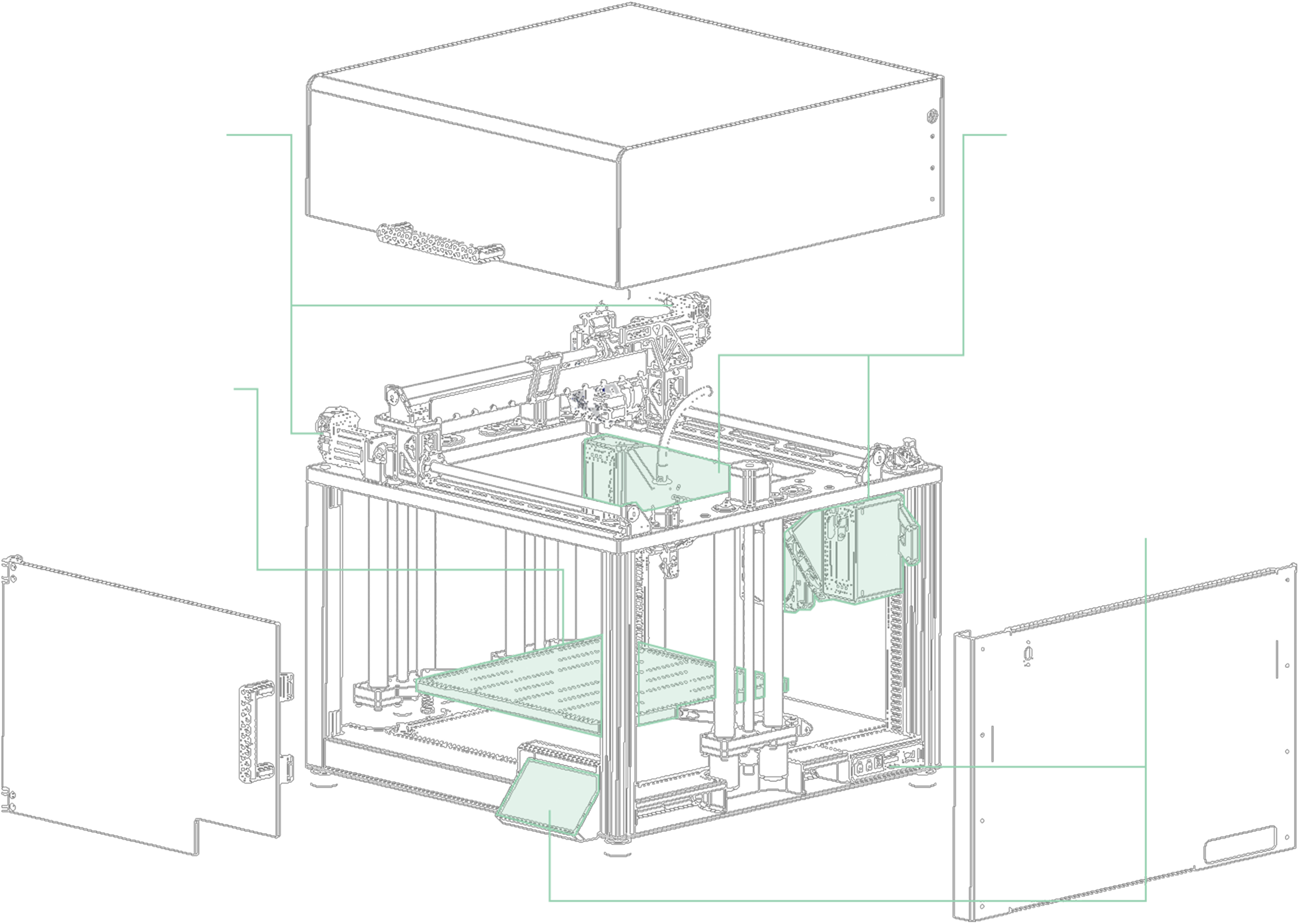
Hot = Strong
Cold to hot in 5 minutes
Don't compromise on quality and speed
Intuitive interface
WIFI + ethernet + USB
Hardware Airgap avalible
Print Big Parts
Materials Overview
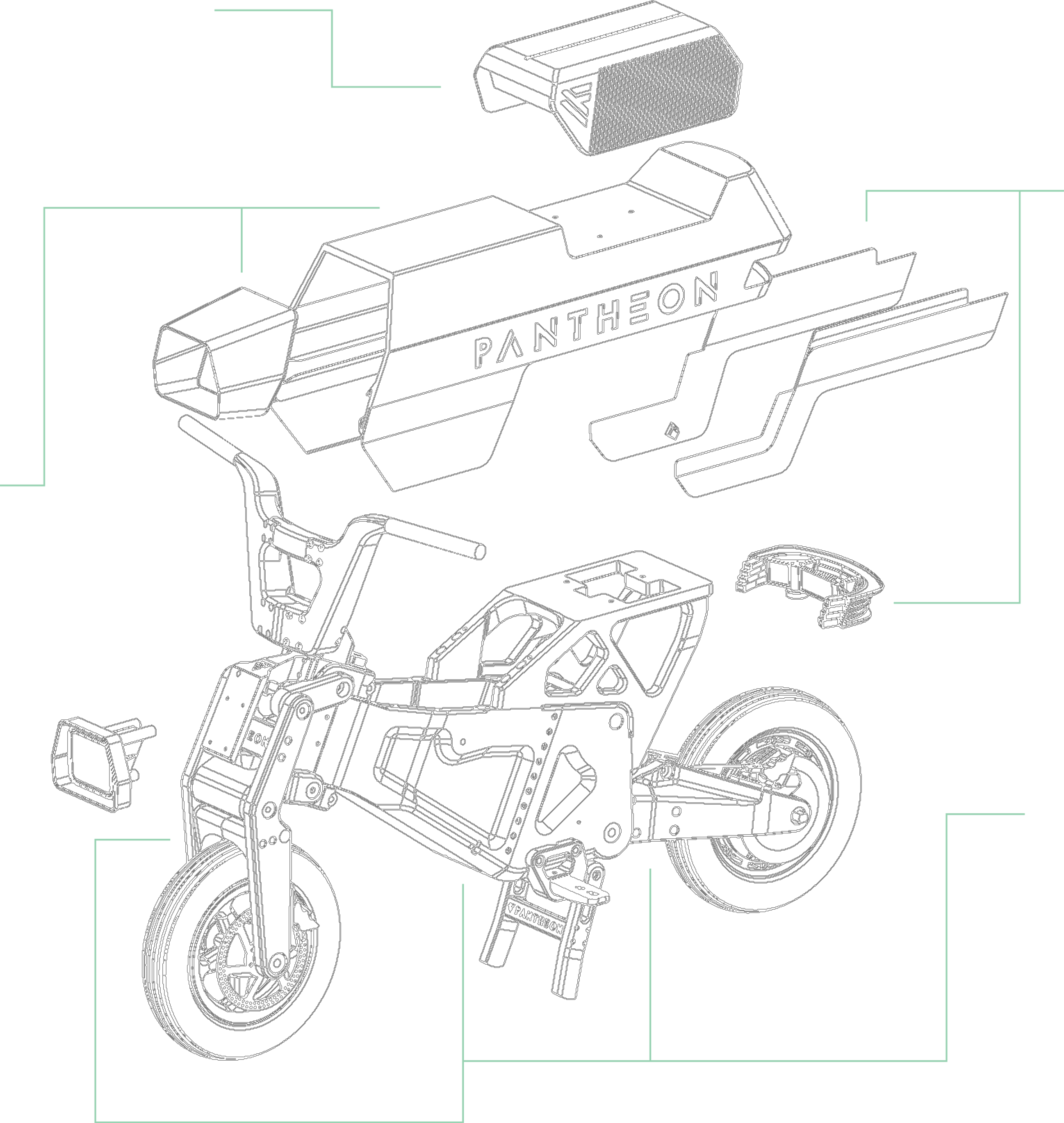
Carbon Fiber PETG
High print speed
95A FLEX
Carbon Fiber Nylon
Glass Fiber Nylon
Good impact Resistance
Strength
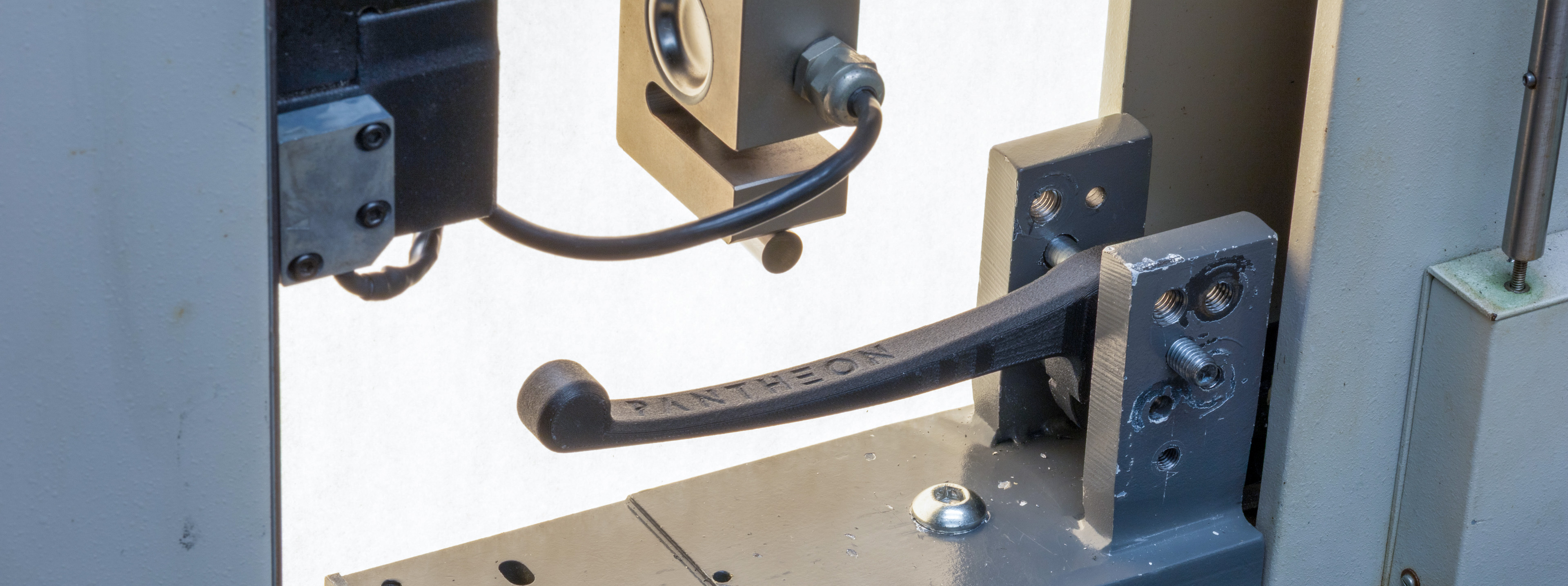
Print Time
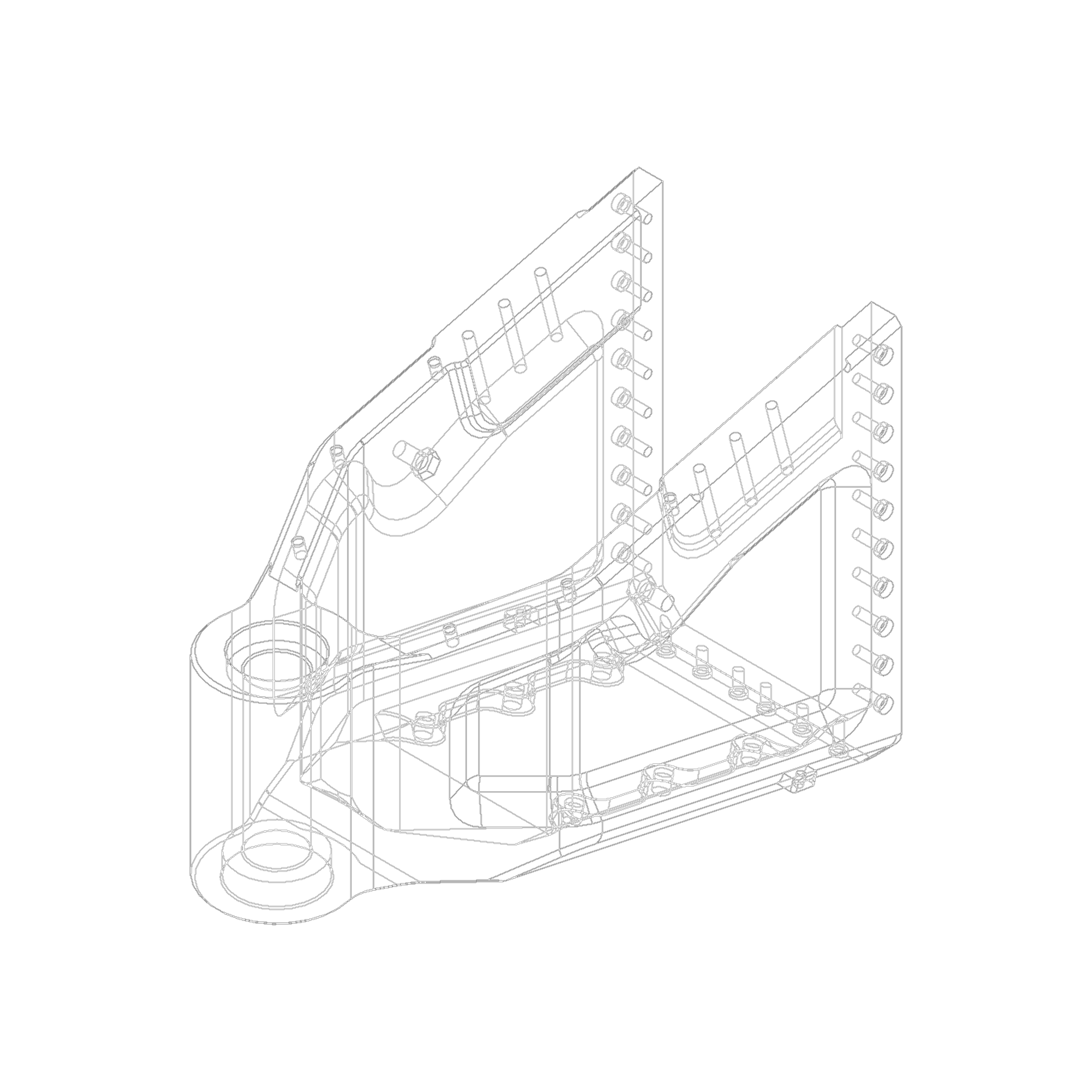
2.26kg in 42hrs
PA12-CF
[x|y|z]: 370x180x265mm
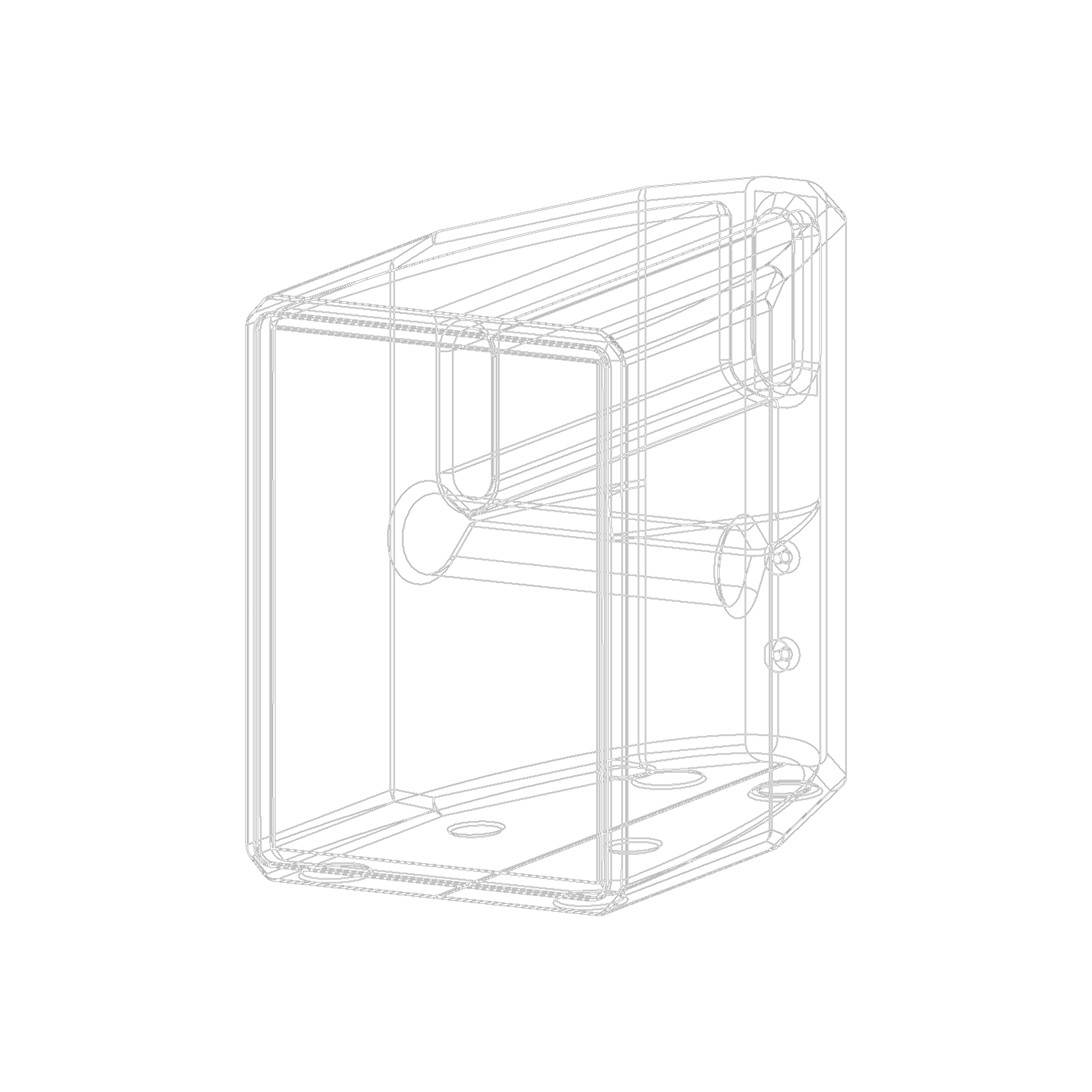
1.41kg in 10hrs
PETG-CF
[x|y|z]: 250x178x245mm
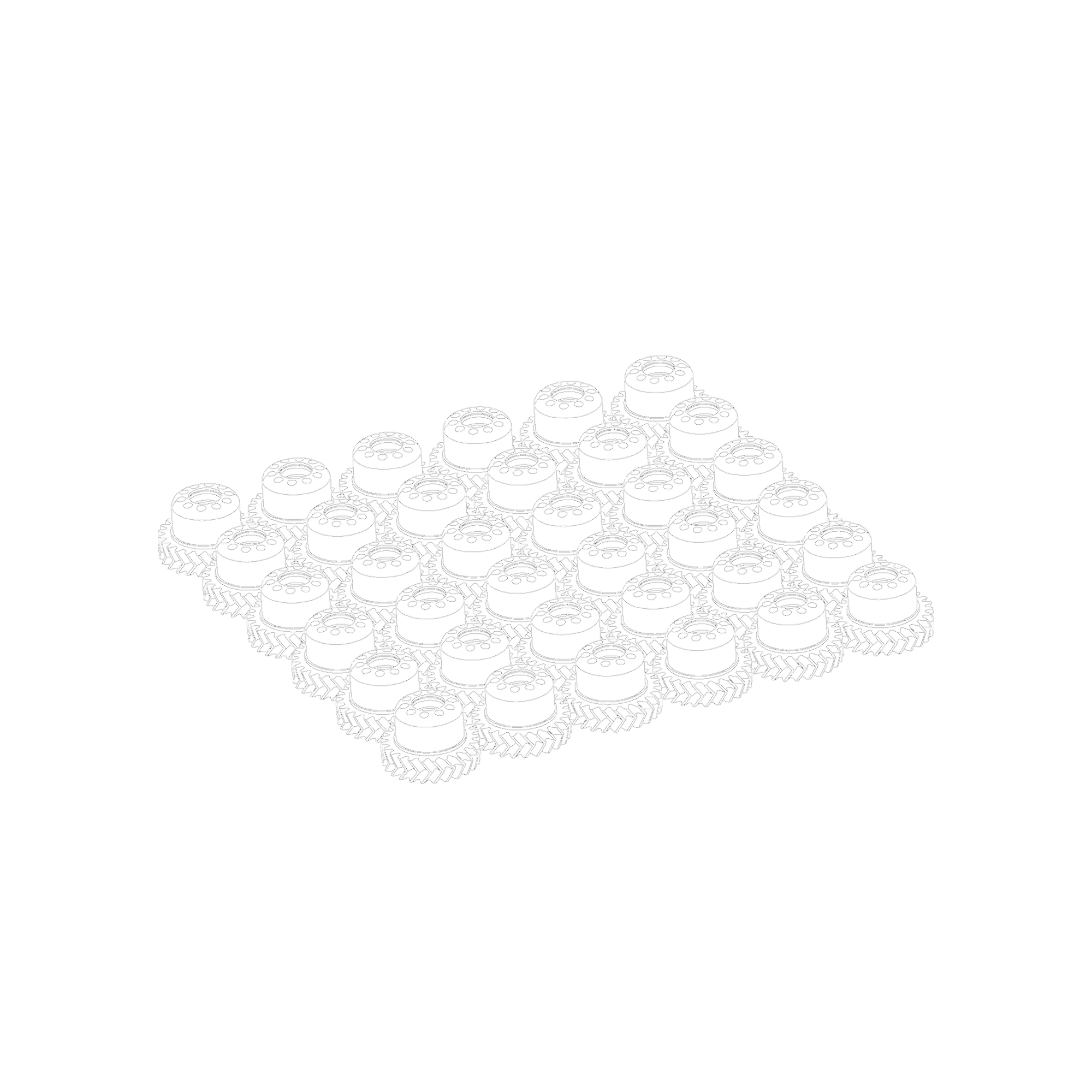
1.73kg in 40 hrs
PA12-GF
[x|y|z]: 64x64x42mm
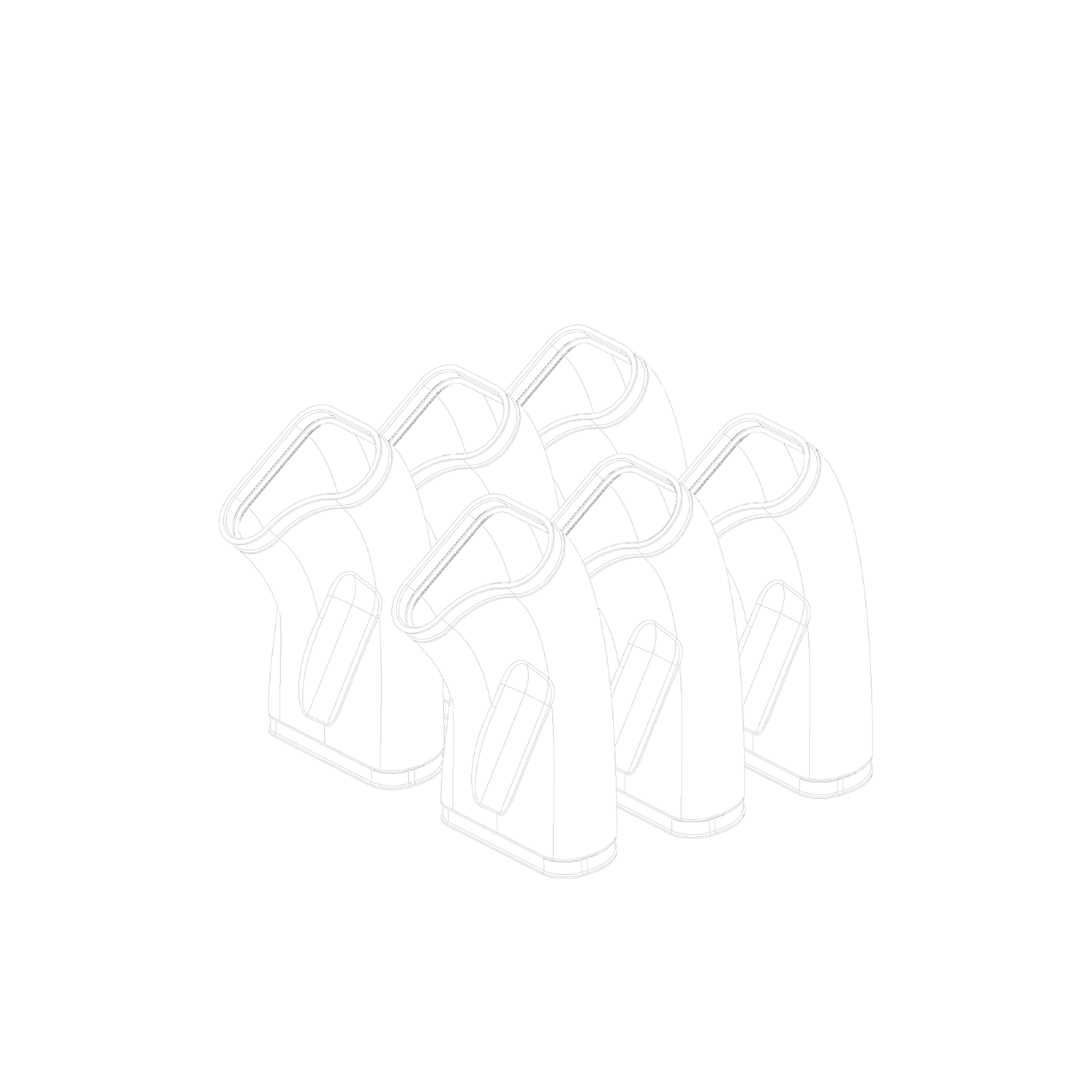
.677kg in 19hrs
95A FLEX
[x|y|z]: 250x178x245mm
Build Volume
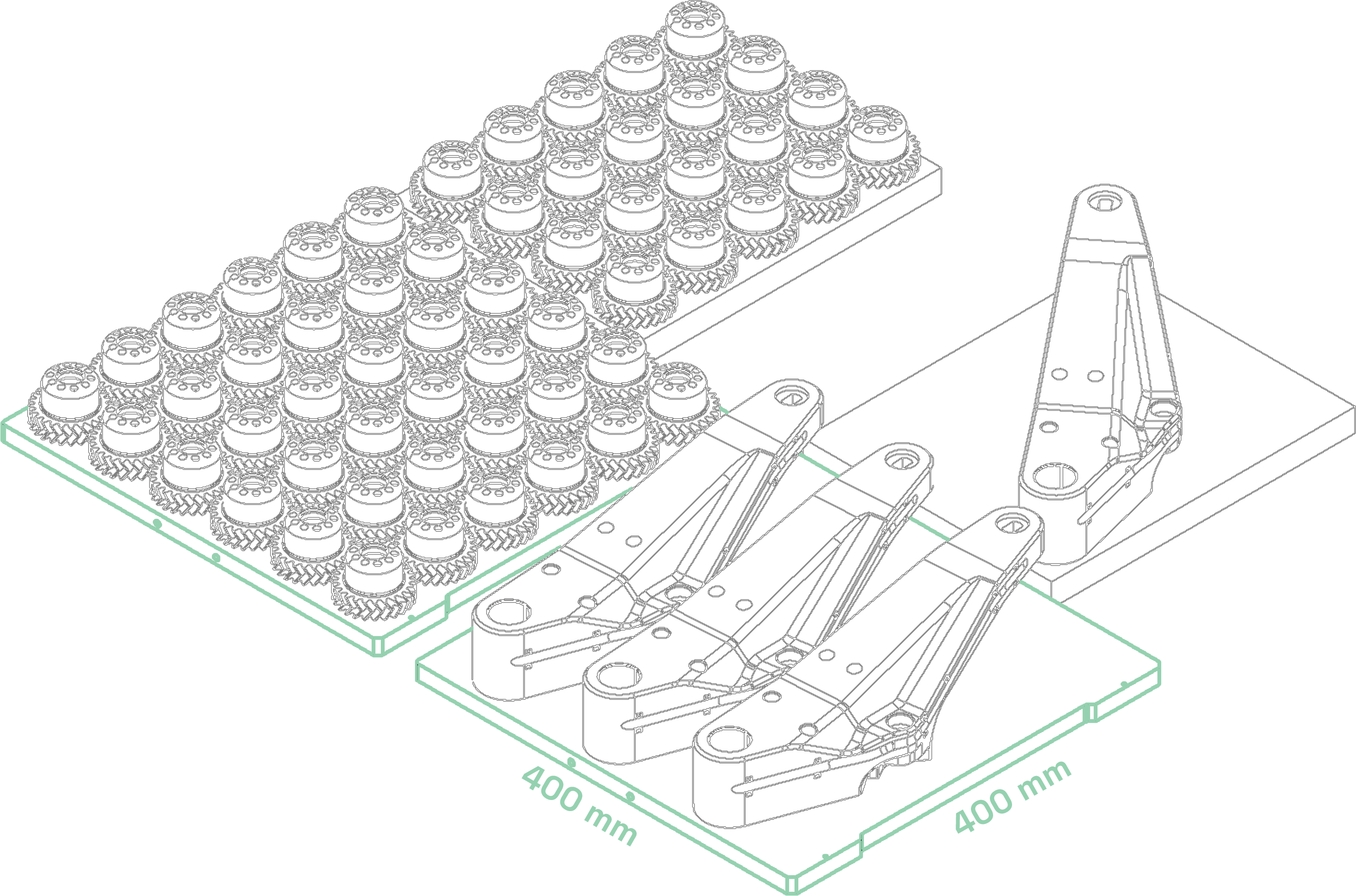
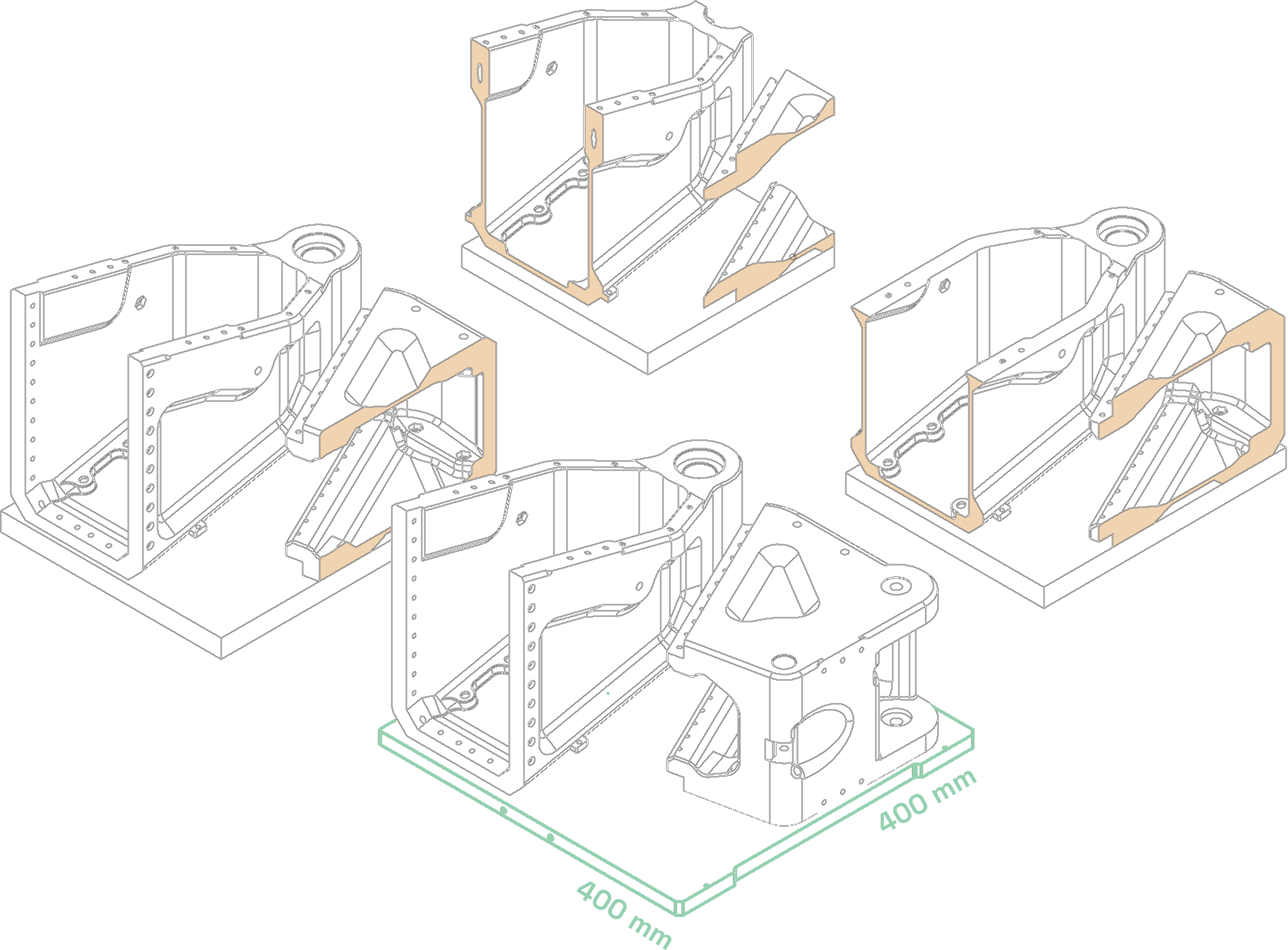
Pantheon Slicer
Mac and Windows support, runs local, unlimited seats, no logins, stupid fast
Multithreaded slicing uses your whole computer's power and means large projects are easy to iterate on
Complete set of G-code visualization and analysis tools shows you exactly what the printer is doing
Every slicing parameter is continuously adjustable, letting you dial in exactly what you want
Mesh and surface part modifiers let you setup parts walls, infill and supports on a per-feature basis
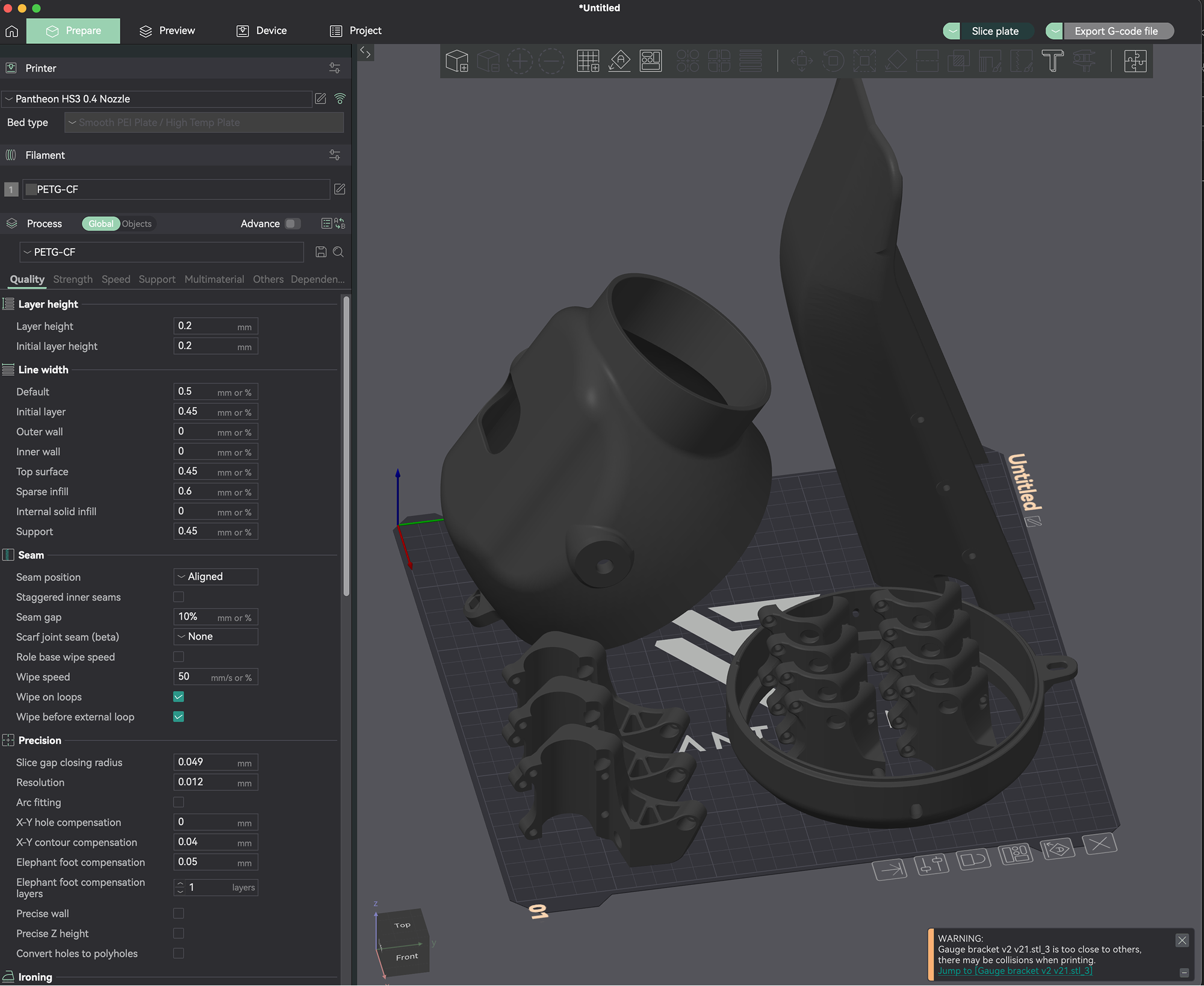
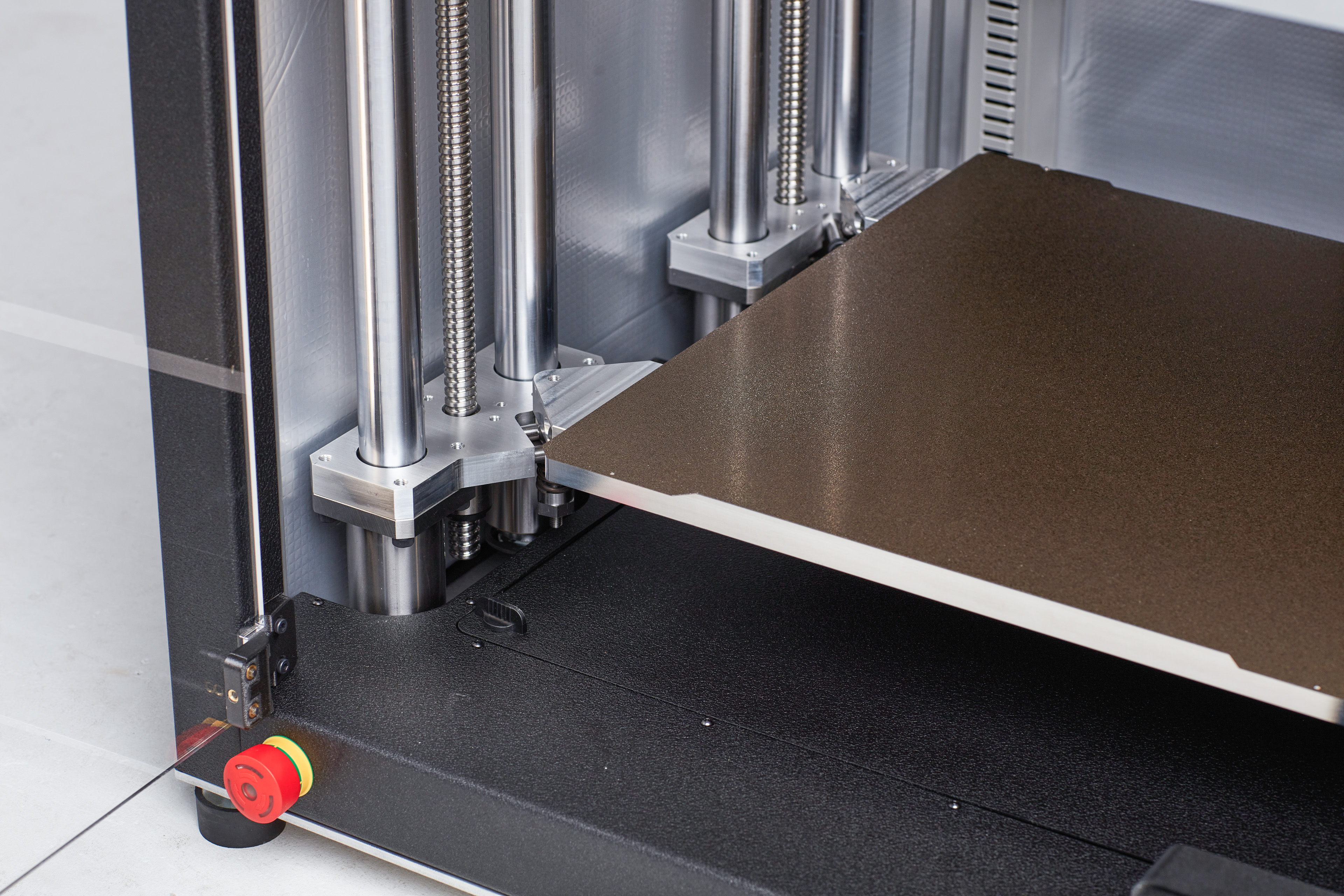
True level
On most printers, the bed is a single Z axis with one degree of freedom. We independently control 3 corners of the bed to allow full software control of bed/printhead alignment.
This means that instead of adjusting for bed-head misalignment in software, we physically move the bed to be parallel to the printhead travel at the start of every print.
This combined with a precision cast aluminum bed surface lets us guarantee part flatness and squareness within 0.050mm.
Printheads are more than just an extruder
A nozzle load cell allows for nozzle probing for the bed for levelling, and in the future print force analysis for realtime quality control.
Onboard STM32 compute module means short analog signal paths and room for lots of sensors. Signal integrity is essential to properly control extrusion.
lightweight billet monoblock construction for the printhead. printhead stiffness is critical to print quality, that's why we use a
All heat must be removed from the part as quickly as it is added by the extruder, no more, no less. We use giant precision-controlled fans to get perfect cooling.
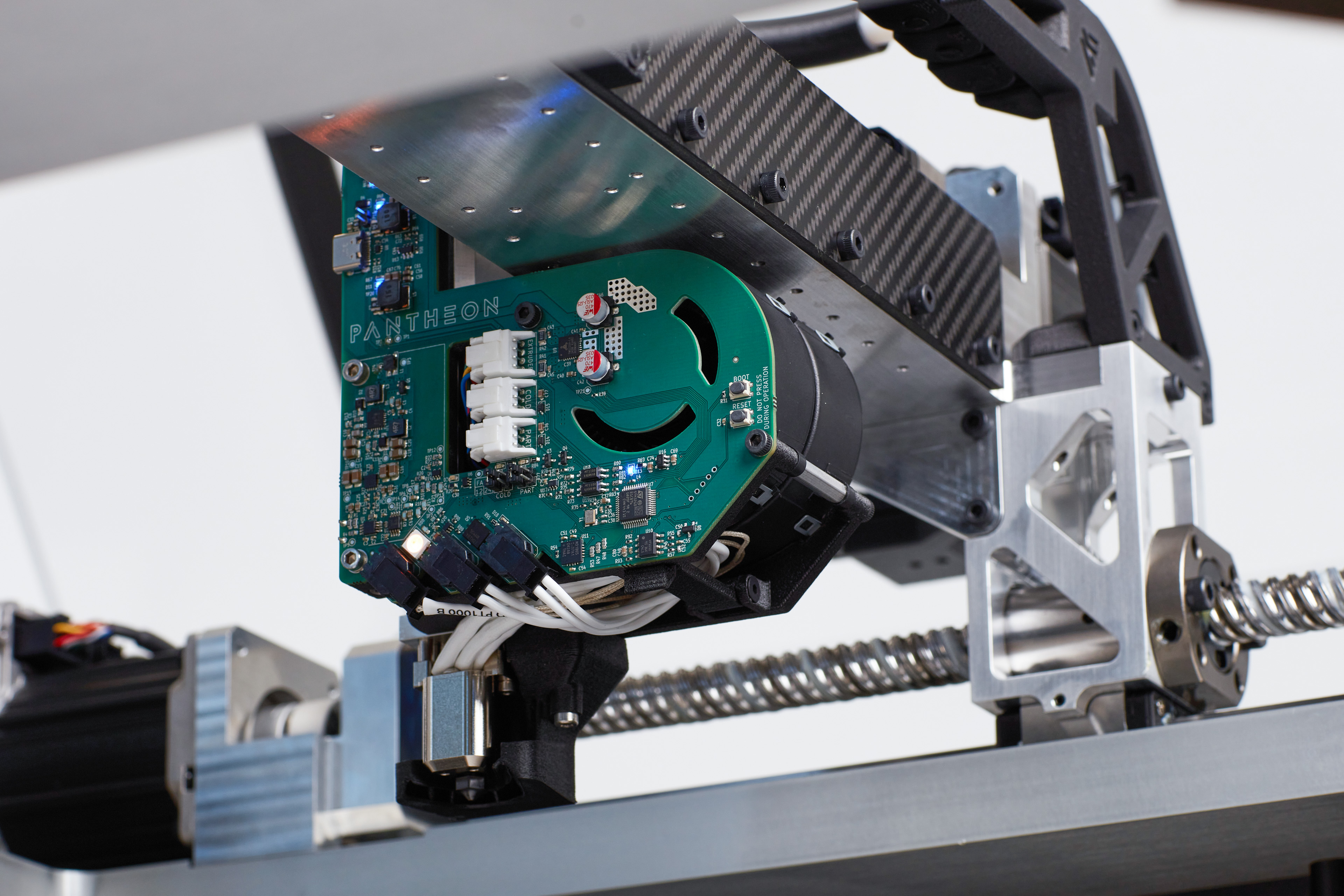
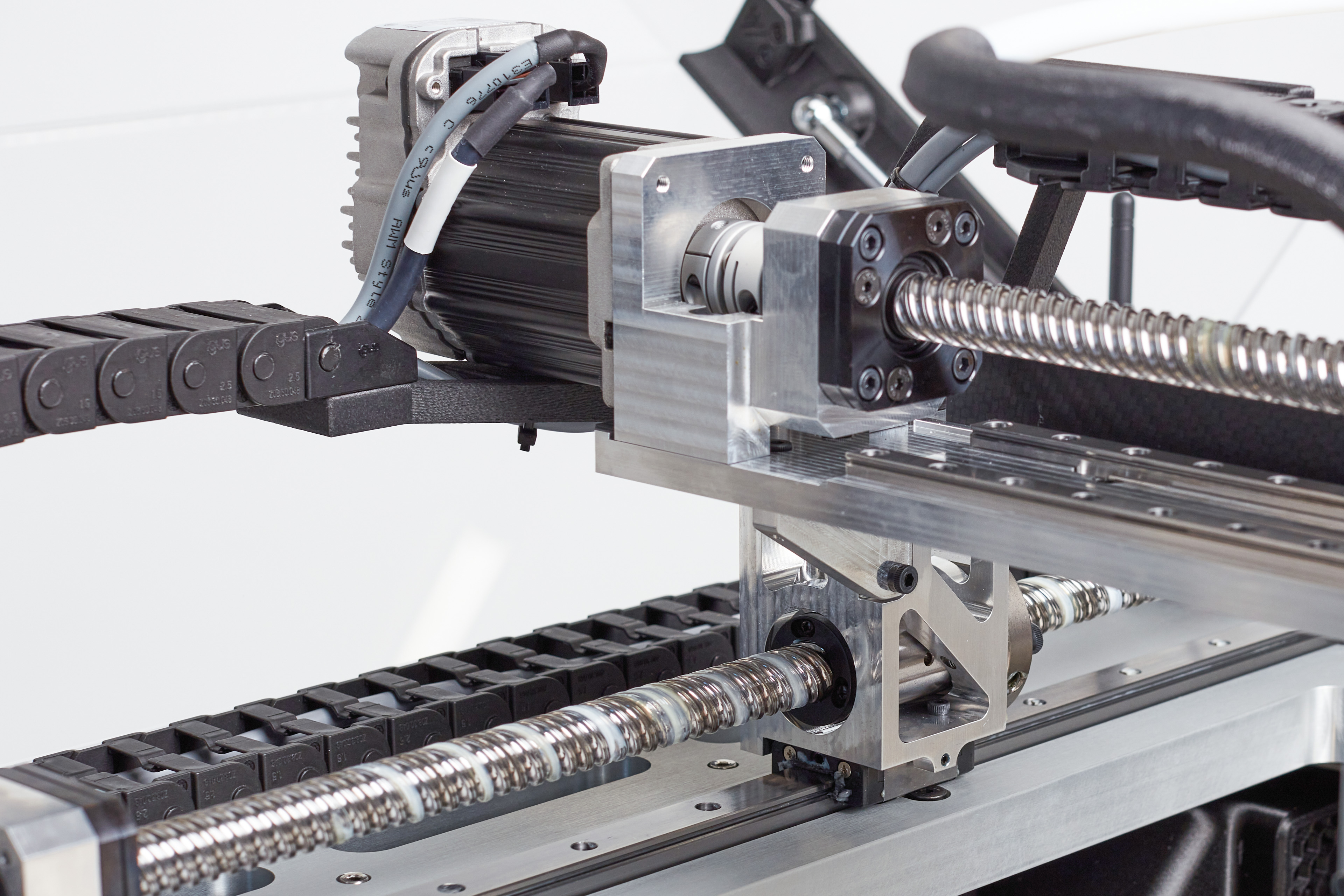
Stepers are bitch ass
Cast aluminum tooling plate with a high-force magnetically-attached build plate. The build tray is kinematically mounted to eliminate warping during heat cycles.
Key Features:
- 16mm thick for thickness
- super flat +/- 20 μm
- 500w 24v heating
- Kelvin kinematic coupling for warp-free heating
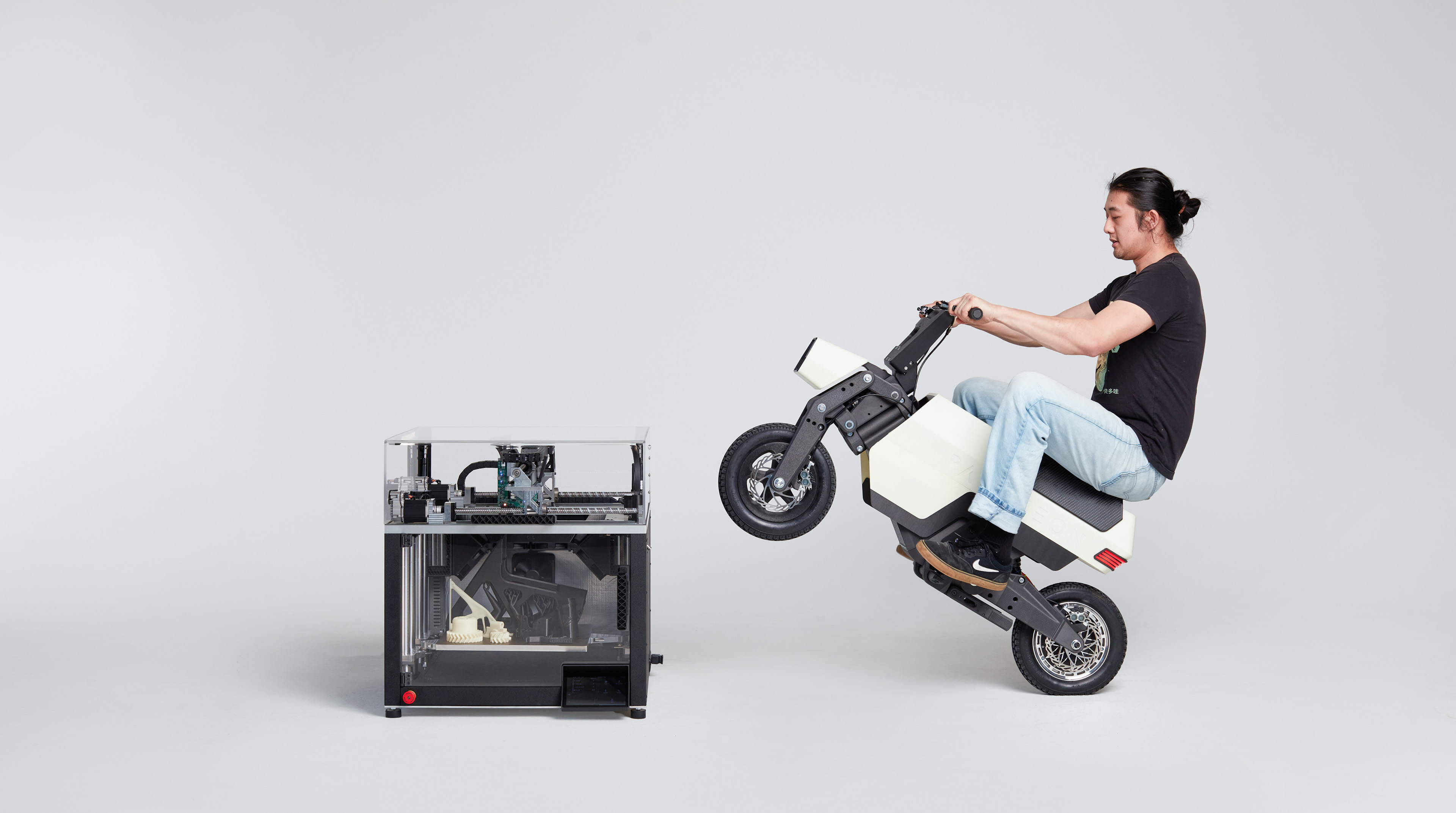
Technologies
Fused Filament Fabrication (FFF)
Patented floating frame system
Carbon-aluminum composite X-spar
Patent-pending nozzle contact probing strain gauge
True level bed
Build Envelope
400mm x 400mm x 300mm
Print Bed
Maxwell kinematic mount
ALCA5 aluminum tooling plate print surface, 20µm flatness
Independent 3-point bed levelling, 20µm tolerance
CNC machined finish
1000W
Build Tray
Removable magnetic spring steel
PEI Coated (smooth and textured available)
Bed Temp
145°C (293°F) Max
Filament Sensor
Mechanically actuated photo gate
Chassis
Topology-optimized Billet 6061 T6 aluminum
Enclosure
Stainless Steel & Acrylic
Chamber
Close loop-controlled temperature to 60°C (140°F) Max
1000W convection heating
Active cooling
Compute
STM32 M0
TMC 2209
Extruder
Billet 6061 T6 Aluminum, 8mm direct-drive hardened steel gears
Hotend
Nickel-plated high temp copper alloy
Hotend Power
120W
Hotend Temp
500°C Max
Temperature Sensor
PT1000 Platinum RTD + MAX31865
Part Cooling
RPM Closed loop controlled Radial Fan
60mm diameter
5 CFM @ 25 mmH20
CFD-optimized cooling duct
Probing
Nozzle contact probing
Patteted controll electronics
Nozzle
0.4mm, 0.5mm and 0.6mm DLC-coated Hardened Steel
0.6mm nickel-plated copper alloy
M6 Thread - 7mm hex
Connectivity
CANBUS
Motors X|Y
Teknik Clearpath Closed Loop DC Servos
Integrated Controllers
Resolution: 0.057°
Repeatability: 0.03°
946W 2.6N-m
Motors Z
Hollow core precision stepper motors
TMC 5160 Drivers
Linear Motion X|Y
C7 preloaded ball screws
X guides: Dual MGN9 light preload
Y guides: Dual MGN15 light preload
Linear Motion Z
Z: C5 Ground preloaded ball screws
Z guides: dual 30mm hollow guides for each stage
Rapid Speeds
750 mm/s
Print Speed
500 mm/s
Acceleration
250,000 mm/s2 <-- this is not a typo
Deposition rate
CF-PETG: 2KG/day avg
CF/GF-Nylon: 1KG/day avg
95A FLEX: 1KG/day
Minimum layer height
0.05mm
Resolution
X-Y: 25 μm
Z: 1.5 μm
Main Computer
Cortex-A72 (ARM v8) 64-bit SoC @ 1.5GHz (upgradeable)
8 GB RAM
32GB eMMC Flash memory
Camera
1080p auto focusing
Architecture
Klipper
Connectivity
100M Ethernet
2.4 GHz, 5.0 GHz IEEE 802.11 b/g/n/ac wireless
CANBUS (internal)
USB
Display
Hi-res 7in IPS touchscreen
Size
machine dimensions (W|D|H):
690mm|785mm|725mm
27.1”|30.9”|28.5”
Height with lid open
1000mm
40 in
Weight
79kg (214lbs)
Operating Temperature Range
15-35°C
Power Supply voltage
100-240V AC, 50/60Hz
Input Power
1800w
Thermal Runaway Cutoff
Thermal Fusing on all AC heaters
Emergency stop button
Replaceable Fuses
Active HEPA+VOC Filtration Available
Install guide
Operating system
Win 7+
Mac OS M1
Mac OS Intel
Linux (source code here, good luck)
Where it runs
local
Supported file formats
STL,STP,3MF,OBJ + more
Multithreading
yes